6. Problem 16-11 (Algo) One of your Taiwanese suppliers has bid on a new line of molded plastic parts that is currently being assembled at your plant. The supplier has bid $0.10 per part, given a forecast you provided of 100,000 parts in year 1; 200,000 in year 2; and 300,000 in year 3. Shipping and handling of parts from the supplier’s factory is estimated at $0.01 per unit. Additional inventory handling charges should amount to $0.005 per unit. Finally, administrative costs are estimated at $20 per month. Although your plant is able to continue producing the part, the plant would need to invest in another molding machine, which would cost $10,000. Direct materials can be purchased for $0.04 per unit. Direct labor is estimated at $0.02 per unit for wages plus a 50 percent surcharge for benefits and, indirect labor is estimated at $0.010 per unit plus 50 percent benefits. Up-front engineering and design costs will amount to $30,000. Finally, management has insisted that overhead be allocated if the parts are made in-house at a rate of 100 percent of direct labor wage costs. The firm uses a cost of capital of 15 percent per year. a. Calculate the difference in NPVs between the Make and Buy options. Express all costs as positive values in your calculations. It is suggested to use the NPV function in Excel. (Do not round intermediate calculations. Round your answer to 2 decimal places.) b. Should you continue to produce in-house or accept the bid from your Taiwanese supplier? multiple choice Accept the bid Correct Produce in-house
6.
Problem 16-11 (Algo)
One of your Taiwanese suppliers has bid on a new line of molded plastic parts that is currently being assembled at your plant. The supplier has bid $0.10 per part, given a
Although your plant is able to continue producing the part, the plant would need to invest in another molding machine, which would cost $10,000. Direct materials can be purchased for $0.04 per unit. Direct labor is estimated at $0.02 per unit for wages plus a 50 percent surcharge for benefits and, indirect labor is estimated at $0.010 per unit plus 50 percent benefits. Up-front engineering and design costs will amount to $30,000. Finally, management has insisted that overhead be allocated if the parts are made in-house at a rate of 100 percent of direct labor wage costs. The firm uses a cost of capital of 15 percent per year.
a. Calculate the difference in NPVs between the Make and Buy options. Express all costs as positive values in your calculations. It is suggested to use the
b. Should you continue to produce in-house or accept the bid from your Taiwanese supplier?
multiple choice
-
Accept the bid Correct
-
Produce in-house

Trending now
This is a popular solution!
Step by step
Solved in 3 steps with 4 images

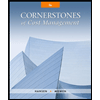
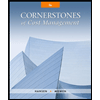