A hollow steel drive shaft working in a high speed machine is shown in the figure and has an outer diameter of 100 mm and a wall thickness of 15 mm. During a particular loading situation, the shaft is subjected to a uniformly distributed load of magnitude 1.75 kN/m and an axial tensile load of magnitude 110 kN as shown. Also, during service, the shaft rotates at a speed of 500 rev/min and transmits a power of 300 kW. The shaft steel is ductile and has a yield strength in tension of 200 MN/m', an ultimate tensile strength of 475 MN/m² and a Modulus of Rigidity of 81 GN/m. Also, the shaft was designed to have a minimum factor of safety of 2. i) Calculate the component stresses set-up in the shaft material at point X' (bottom surface of the shaft at midspan as indicated in the figure) due to the loading conditions. ii) Determine the magnitude and nature of the principal stresses, and the maximum shear stress analytically and graphically, and the angle of the planes on which the major principal stresses act at point X'. iii) By applying the appropriate yield criteria, evaluate the factor of safety for the shaft and
A hollow steel drive shaft working in a high speed machine is shown in the figure and has an outer diameter of 100 mm and a wall thickness of 15 mm. During a particular loading situation, the shaft is subjected to a uniformly distributed load of magnitude 1.75 kN/m and an axial tensile load of magnitude 110 kN as shown. Also, during service, the shaft rotates at a speed of 500 rev/min and transmits a power of 300 kW. The shaft steel is ductile and has a yield strength in tension of 200 MN/m', an ultimate tensile strength of 475 MN/m² and a Modulus of Rigidity of 81 GN/m. Also, the shaft was designed to have a minimum factor of safety of 2. i) Calculate the component stresses set-up in the shaft material at point X' (bottom surface of the shaft at midspan as indicated in the figure) due to the loading conditions. ii) Determine the magnitude and nature of the principal stresses, and the maximum shear stress analytically and graphically, and the angle of the planes on which the major principal stresses act at point X'. iii) By applying the appropriate yield criteria, evaluate the factor of safety for the shaft and
Mechanics of Materials (MindTap Course List)
9th Edition
ISBN:9781337093347
Author:Barry J. Goodno, James M. Gere
Publisher:Barry J. Goodno, James M. Gere
Chapter11: Columns
Section: Chapter Questions
Problem 11.3.10P: Repeat Problem 11.3-9. Use two C 150 × 12.2 steel shapes and assume that E = 205 GPa and L = 6 m.
Related questions
Question
Please help answer this question

Transcribed Image Text:A hollow steel drive shaft working in a high speed machine is shown in the figure and has an
outer diameter of 100 mm and a wall thickness of 15 mm. During a particular loading situation,
the shaft is subjected to a uniformly distributed load of magnitude 1.75 kN/m and an axial
tensile load of magnitude 110 kN as shown. Also, during service, the shaft rotates at a speed of
500 rev/min and transmits a power of 300 kW.
The shaft steel is ductile and has a yield strength in tension of 200 MN/m, an ultimate tensile
strength of 475 MN/m² and a Modulus of Rigidity of 81 GN/m. Also, the shaft was designed
to have a minimum factor of safety of 2.
Calculate the component stresses set-up in the shaft material at point 'X' (bottom surface
of the shaft at midspan as indicated in the figure) due to the loading conditions.
ii) Determine the magnitude and nature of the principal stresses, and the maximum shear
stress analytically and graphically, and the angle of the planes on which the major
principal stresses act at point X'.
ii) By applying the appropriate yield criteria, evaluate the factor of safety for the shaft and
comment on the value obtained.
iv) Produce a neat sketch of the yield criteria failure envelopes for the shaft at point X',
indicating all significant detail.
v) Given that the shaft outer surface has a 'machined' finish and the shaft operates at a
temperature of 85°C and a reliability of 95% is required, determine the factor of safety for
the shaft according to the Soderberg theory, commenting on its value.
vi) During another loading operation, the shaft is subjected to excessive bending loading
conditions that cause the major principal stress to increase to 175 MN/m?. Determine the
life expectancy of the shaft.
vii) Calculate the total strain energy stored in the shaft during the initial loading.
i)

Transcribed Image Text:D=100 mm
1.75 kN/m
110 kN
110 kN
2.5 m
t=15 mm
Shaft Cross-Section
Dimensions
Expert Solution

This question has been solved!
Explore an expertly crafted, step-by-step solution for a thorough understanding of key concepts.
This is a popular solution!
Trending now
This is a popular solution!
Step by step
Solved in 7 steps with 3 images

Knowledge Booster
Learn more about
Need a deep-dive on the concept behind this application? Look no further. Learn more about this topic, mechanical-engineering and related others by exploring similar questions and additional content below.Recommended textbooks for you
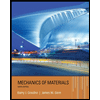
Mechanics of Materials (MindTap Course List)
Mechanical Engineering
ISBN:
9781337093347
Author:
Barry J. Goodno, James M. Gere
Publisher:
Cengage Learning
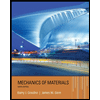
Mechanics of Materials (MindTap Course List)
Mechanical Engineering
ISBN:
9781337093347
Author:
Barry J. Goodno, James M. Gere
Publisher:
Cengage Learning