Fruit-To-Go (FTG) processes fruit for shipping overseas. FTG commissioned a study to look into the feasibility of changing the packaging of the fruit from cans to sealed bags. The Consultant charged $54,000 for the report. The report concluded that the new packaging will increase sales and reduce some operating costs. The new packaging machinery will cost $1,100,000. The new machine is expected to last 5 years. The Taxation Office advise the life of the machine, for tax purposes, is 4 years. The old canning machinery was purchased 2 years ago for $800,000 and was being depreciated at The old canning machinery was purchased 2 years ago for $800,000 and was being depreciated at $200,000 and will be for the next 2 years. The old machine could be sold today for $260,000. In 5 years it will be worth nothing. Installing the new machine will require staff training (a tax deductible expense) of $35,000 before production can commence. Due to the lower cost of the bags Inventory required will be reduced by $80,000 for the life of the project. The new sales of bagged fruit is expected to be $700,000 in Year 1 rising by 15% for 2 years then 0% for the rest of the life of the pr The new sales of bagged fruit is expected to be $700,000 in Year 1 rising by 15% for 2 years then 0% for the rest of the life of the project. Variable Costs associated with the new packaged fruit are 50% of sales. Canned fruit production will be discontinued. Sales of canned fruit were static at $450,000 with variable costs of $225,000 (50% of Sales). The new equipment is very hi-tech. Maintenance costs are expected to be higher at $44,000 per year. Maintenance costs on the old machine were $30,000 per year. The lighter packaging will reduce annual freight cost significantly from $250,000 to $100,000 per year. Fixed costs are expected to remain at $320,000 per year. At the end of the project the new machinery can be sold for $275,000. Notes: FTG will borrow the full Year 0 funds using a secured five-year interest-only loan at an interest rate of 10% per annum to finance the new equipment. The company tax rate is 30%. The required rate of return is 12.5%. Requirement: You are required to answer and to conduct a capital budgeting analysis of the company. You must determine: 1. The cash flows at the start 2. The cash flows over the life 3. The cash flows at the end
Fruit-To-Go (FTG) processes fruit for shipping overseas.
FTG commissioned a study to look into the feasibility of changing the packaging of the fruit from cans to sealed bags. The Consultant charged $54,000 for the report.
The report concluded that the new packaging will increase sales and reduce some operating costs.
The new packaging machinery will cost $1,100,000. The new machine is expected to last 5 years. The
The old canning machinery was purchased 2 years ago for $800,000 and was being
Installing the new machine will require staff training (a tax deductible expense) of $35,000 before production can commence. Due to the lower cost of the bags Inventory required will be reduced by $80,000 for the life of the project.
The new sales of bagged fruit is expected to be $700,000 in Year 1 rising by 15% for 2 years then 0% for the rest of the life of the pr
The new sales of bagged fruit is expected to be $700,000 in Year 1 rising by 15% for 2 years then 0% for the rest of the life of the project. Variable Costs associated with the new packaged fruit are 50% of sales.
Canned fruit production will be discontinued. Sales of canned fruit were static at $450,000 with variable costs of $225,000 (50% of Sales).
The new equipment is very hi-tech. Maintenance costs are expected to be higher at $44,000 per year. Maintenance costs on the old machine were $30,000 per year.
The lighter packaging will reduce annual freight cost significantly from $250,000 to $100,000 per year.
Fixed costs are expected to remain at $320,000 per year.
At the end of the project the new machinery can be sold for $275,000.
Notes:
FTG will borrow the full Year 0 funds using a secured five-year interest-only loan at an interest rate of 10% per annum to finance the new equipment.
The company tax rate is 30%.
The required rate of return is 12.5%.
Requirement:
You are required to answer and to conduct a capital budgeting analysis of the company. You must determine:
1. The cash flows at the start
2. The cash flows over the life
3. The cash flows at the end
4. The appropriate discount rate
5. The
6. The
7. The PI of the project
8. The payback of the project
9. A brief recommendation
10. Please give short explanation on how to make investing decision.

Trending now
This is a popular solution!
Step by step
Solved in 2 steps

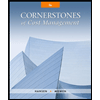
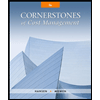