Vapor Composition, Mole Fraction BENZENE 1 0.9 0.8 0.7 0.6 0.5 0.4 0.3 0.2 0.1 For part a) For part b) 0 feed has 49.1 mol % benzene and overhead product has 96.6 mol % benzene (bottoms product concentration remains unchanged at 2.35 mol %) feed rate F is 352.4 kg mol/hr i) remains unchanged - feed is liquid at boiling point ii) feed is liquid at 25 °C iii) feed is a mixture with 3/5 vapor and 2/5 liquid X-Y Plot for BENZENE and TOLUENE (Thermo = UNIF01, P = 1.0000 atm) 0.2 0.4 0.6 Liquid Composition, Mole Fraction BENZENE 0.8 1 <-x=y - Equilibrium curve
Vapor Composition, Mole Fraction BENZENE 1 0.9 0.8 0.7 0.6 0.5 0.4 0.3 0.2 0.1 For part a) For part b) 0 feed has 49.1 mol % benzene and overhead product has 96.6 mol % benzene (bottoms product concentration remains unchanged at 2.35 mol %) feed rate F is 352.4 kg mol/hr i) remains unchanged - feed is liquid at boiling point ii) feed is liquid at 25 °C iii) feed is a mixture with 3/5 vapor and 2/5 liquid X-Y Plot for BENZENE and TOLUENE (Thermo = UNIF01, P = 1.0000 atm) 0.2 0.4 0.6 Liquid Composition, Mole Fraction BENZENE 0.8 1 <-x=y - Equilibrium curve
Introduction to Chemical Engineering Thermodynamics
8th Edition
ISBN:9781259696527
Author:J.M. Smith Termodinamica en ingenieria quimica, Hendrick C Van Ness, Michael Abbott, Mark Swihart
Publisher:J.M. Smith Termodinamica en ingenieria quimica, Hendrick C Van Ness, Michael Abbott, Mark Swihart
Chapter1: Introduction
Section: Chapter Questions
Problem 1.1P
Related questions
Question

Transcribed Image Text:EXAMPLE 21.2. A continuous fractionating column is to be designed to separate
30,000 kg/h of a mixture of 40 percent benzene and 60 percent toluene into an overhead
product containing 97 percent benzene and a bottom product containing 98 percent
toluene. These percentages are by weight. A reflux ratio of 3.5 mol to 1 mol of product is
to be used. The molal latent heats of benzene and toluene are 7,360 and 7,960 cal/g mol,
respectively. Benzene and toluene form a nearly ideal system with a relative volatility of
about 2.5; the equilibrium curve is shown in Fig. 21.14. The feed has a boiling point of
95°C at a pressure of 1 atm. (a) Calculate the moles of overhead product and bottom
product per hour. (b) Determine the number of ideal plates and the position of the feed
plate (i) if the feed is liquid and at its boiling point; (ii) if the feed is liquid and at 20°C
(specific heat 0.44 cal/g. °C); (iii) if the feed is a mixture of two-thirds vapor and one-
third liquid. (c) If steam at 20 lb/in.² (1.36 atm) gauge is used for heating, how much
steam is required per hour for each of the above three cases, neglecting heat losses and
assuming the reflux is a saturated liquid? (d) If cooling water enters the condenser at
25°C and leaves at 40°C, how much cooling water is required, in cubic meters per hour?
Solution
(a) The molecular weight of benzene is 78, and that of toluene is 92. The concen-
trations of feed, overhead, and bottoms in mole fraction of benzene are
0.216
XF=
11
XB
10
|
40
78
40 60
78 92
FIGURE 21 14
+
9
= 0.440
XB =
8
78
XF
X
XD =
97
78
97
78
5
+ 3/2
= 0.0235
Feed line
= 0.974
XD
The average molecular weight of the feed is
100
60
40+50
78
92
= 85.8
The average heat of vaporization of the feed is
λ = 0.44(7,360) +0.56(7,960) = 7,696 cal/g mol
The feed rate F is 30,000/85.8= 350 kg mol/h. By an overall benzene balance, using
Eq. (21.8),
D = 350
0.440 0.0235
0.974 -0.0235
= 153.4 kg mol/h
B = 350 153.4 = 196.6 kg mol/h
(b) Next we determine the number of ideal plates and position of the feed plate.
(i) The first step is to plot the equilibrium diagram and on it erect verticals at Xp, X
and xp. These should be extended to the diagonal of the diagram. Refer to Fig. 21.14
The second step is to draw the feed line. Here f = 0, and the feed line is vertical and is
a continuation of line x = xF. The third step is to plot the operating lines. The intercept
of the rectifying line on the y axis is, from Eq. (21.22), 0.974/(3.5+ 1) = 0.216. This
point is connected with the point x, on the yx reference line. From the intersection of the
rectifying operating line and the feed line, the stripping line is drawn.
The fourth step is to draw the rectangular steps between the two operating lines and
the equilibrium curve. In drawing the steps, the transfer from the rectifying line to the
stripping line is at the seventh step. By counting steps it is found that, besides the
reboiler, 11 ideal plates are needed and feed should be introduced on the seventh plate
from the top.
is 7,696/85.8= 89.7 cal/g. Sub-
(ii) The latent heat of vaporization of the feed
stitution in Eq. (21.27) gives
q=1+
0.44(95-20)
89.7
= 1.37
From Eq. (21.34) the slope of the feed line is -1.37/(1-1.37) = 3.70. When steps
are drawn for this case, as shown in Fig. 21.15, it is found that a reboiler and 10 ideal
plates are needed and that the feed should be introduced on the sixth plate.
(iii) From the definition of q it follows that for this case q = and the slope of the
feed line is -0.5. The solution is shown in Fig. 21.16. It calls for a reboiler and
12 plates, with the feed entering on the seventh plate.
More plates are needed when the feed is largely vapor, partly because the feed line
Islants to the left and a few more plates are required in the rectifying section. The major
reason, however, is that partially vaporized feed contributes less liquid to the stripping
section than does a totally liquid feed, and the reflux ratio in the stripping section is
reduced.
To fulfill the conditions of the problem literally, the last step, which represents the reboiler, should
reach the concentration XB exactly. This is nearly true in Fig. 21.14. Usually, xg does not correspond to
an integral number of steps. An arbitrary choice of the four quantities Xp, X, X, and R, is not necessar-
ily consistent with an integral number of steps. An integral number can be obtained by a slight adjust-
the actual number of plates is established there is little reason for making this adjustment.
ment of one of the four quantities, but in view of the fact that a plate efficiency must be applied before
0.216
10.
0.216
XB
FIGURE 21.15
Example 21.2, part (b)(ii).
XB
8.
10
Feed line
9
8
1
FIGURE 21.16
Example 21 2. part (b)(iii).
XF
XF
X-
Feed line
3
3
XD
1
1
XD

Transcribed Image Text:Repeat Example 21.2 parts a) and b) (MSH (textbook) p. 683-685) with the following changes:
For part a)
Vapor Composition, Mole Fraction BENZENE
1
0.9
0.8
0.7
0.6
0.5
0.4
0.3
0.2
0.1
0
For part b)
0
feed has 49.1 mol % benzene and overhead product has 96.6 mol % benzene
(bottoms product concentration remains unchanged at 2.35 mol %)
feed rate F is 352.4 kg mol/hr
i) remains unchanged - feed is liquid at boiling point
ii) feed is liquid at 25 °C
iii) feed is a mixture with 3/5 vapor and 2/5 liquid
X-Y Plot for BENZENE and TOLUENE (Thermo = UNIF01,
P = 1.0000 atm)
0.2
0.4
0.6
Liquid Composition, Mole Fraction BENZENE
0.8
1
-x=y
Equilibrium curve
Expert Solution

This question has been solved!
Explore an expertly crafted, step-by-step solution for a thorough understanding of key concepts.
This is a popular solution!
Trending now
This is a popular solution!
Step by step
Solved in 6 steps with 4 images

Recommended textbooks for you
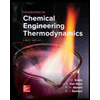
Introduction to Chemical Engineering Thermodynami…
Chemical Engineering
ISBN:
9781259696527
Author:
J.M. Smith Termodinamica en ingenieria quimica, Hendrick C Van Ness, Michael Abbott, Mark Swihart
Publisher:
McGraw-Hill Education
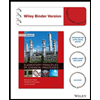
Elementary Principles of Chemical Processes, Bind…
Chemical Engineering
ISBN:
9781118431221
Author:
Richard M. Felder, Ronald W. Rousseau, Lisa G. Bullard
Publisher:
WILEY
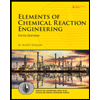
Elements of Chemical Reaction Engineering (5th Ed…
Chemical Engineering
ISBN:
9780133887518
Author:
H. Scott Fogler
Publisher:
Prentice Hall
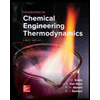
Introduction to Chemical Engineering Thermodynami…
Chemical Engineering
ISBN:
9781259696527
Author:
J.M. Smith Termodinamica en ingenieria quimica, Hendrick C Van Ness, Michael Abbott, Mark Swihart
Publisher:
McGraw-Hill Education
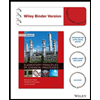
Elementary Principles of Chemical Processes, Bind…
Chemical Engineering
ISBN:
9781118431221
Author:
Richard M. Felder, Ronald W. Rousseau, Lisa G. Bullard
Publisher:
WILEY
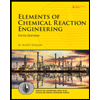
Elements of Chemical Reaction Engineering (5th Ed…
Chemical Engineering
ISBN:
9780133887518
Author:
H. Scott Fogler
Publisher:
Prentice Hall
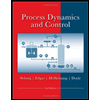
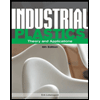
Industrial Plastics: Theory and Applications
Chemical Engineering
ISBN:
9781285061238
Author:
Lokensgard, Erik
Publisher:
Delmar Cengage Learning
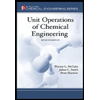
Unit Operations of Chemical Engineering
Chemical Engineering
ISBN:
9780072848236
Author:
Warren McCabe, Julian C. Smith, Peter Harriott
Publisher:
McGraw-Hill Companies, The