Drew Castello, general manager of Sunflower Manufacturing, was frustrated. He wanted the budgeted results, and his staff was not getting them to him fast enough. Drew decided to pay a visit to the accounting office, where Jeff Hollingsworth was supposed to be working on the reports. Jeff had recently been hired to update the accounting system and speed up the reporting process. "What's taking so long?" Drew asked. “When am I going to get the variance reports?" Jeff sighed and attempted to explain the problem. "Some of the variances appear to be way off. We either have a serious problem in production, or there is an error in the spreadsheet. I want to recheck the spreadsheet before I distribute the report." Drew pulled up a chair, and the two men went through the spreadsheet together. The formulas in the spreadsheet were correct and showed a large unfavorable direct labor efficiency variance. It was time for Drew and Jeff to do some investigating. After looking at the time records, Jeff pointed out that it was unusual that every employee in the production area recorded exactly eight hours each day in direct labor. Did they not take breaks? Was no one ever five minutes late getting back from lunch? What about clean-up time between jobs or at the end of the day? Drew began to observe the production laborers and noticed several disturbing items. One employee was routinely late for work, but his time card always showed him clocked in on time. Another employee took 10- to 15-minute breaks every hour, averaging about one and a half hours each day, but still reported eight hours of direct labor each day. Yet another employee often took an extra 30 minutes for lunch, but his time card showed him clocked in on time. No one in the production area ever reported any "down time" when they were not working on a specific job, even though they all took breaks and completed other tasks such as doing clean-up and attending department meetings. Requirements 1. How might the observed behaviors cause an unfavorable direct labor efficiency variance? 2. How might an employee's time card show the employee on the job and working when the employee was not present? 3. Why would the employees' activities be considered fraudulent?
Critical Path Method
The critical path is the longest succession of tasks that has to be successfully completed to conclude a project entirely. The tasks involved in the sequence are called critical activities, as any task getting delayed will result in the whole project getting delayed. To determine the time duration of a project, the critical path has to be identified. The critical path method or CPM is used by project managers to evaluate the least amount of time required to finish each task with the least amount of delay.
Cost Analysis
The entire idea of cost of production or definition of production cost is applied corresponding or we can say that it is related to investment or money cost. Money cost or investment refers to any money expenditure which the firm or supplier or producer undertakes in purchasing or hiring factor of production or factor services.
Inventory Management
Inventory management is the process or system of handling all the goods that an organization owns. In simpler terms, inventory management deals with how a company orders, stores, and uses its goods.
Project Management
Project Management is all about management and optimum utilization of the resources in the best possible manner to develop the software as per the requirement of the client. Here the Project refers to the development of software to meet the end objective of the client by providing the required product or service within a specified Period of time and ensuring high quality. This can be done by managing all the available resources. In short, it can be defined as an application of knowledge, skills, tools, and techniques to meet the objective of the Project. It is the duty of a Project Manager to achieve the objective of the Project as per the specifications given by the client.


Trending now
This is a popular solution!
Step by step
Solved in 2 steps

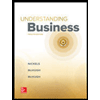
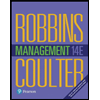
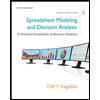
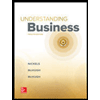
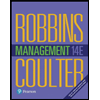
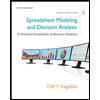
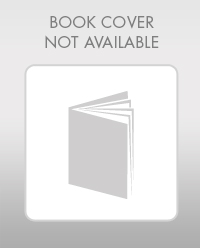
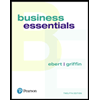
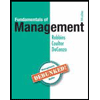