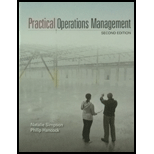
Concept explainers
a
Interpretation:
Amount paid by the hotel for desert and frequency of production of desert under its current policy.
Concept Introduction: Materials Requirement Planning is a process in which planning is made for the requirement of raw material required for manufacturing of the finished product.
a

Explanation of Solution
Demand for desert = 30,000 per year
Production rate = 125 per day
Set up cost = $4
Cost of dessert = $0.40
Daily demand for dessert is calculated by dividing annual demand with the number of days the company can operate in the year.
Hence, the daily demand is 82 desserts.
Calculation of holding cost.
It is given that holding cost is 300% of the cost of the dessert.
Hence, the holding cost per dessert is $1.2
Calculation of total holding and ordering cost for given batch quantity.
It is given that the current batch quantity is 300 desserts.
Calculation of annual holding cost:
Annual holding cost is calculated by multiplying the holding cost with two values. First value is calculated by dividing the quantity with 2. Second value is calculated by subtracting the value attained by dividing the daily demand with the production from 1.
Hence, the annual holding cost is $61.92
Calculation of annual ordering cost:
It is calculated by multiplying the setup cost with the value attained by dividing the annual demand with the batch quantity.
Hence, the annual ordering cost is $400.
Calculation of total cost of inventory:
It is calculated by adding the annual holding cost and annual ordering cost.
Hence, the total cost of inventory is $461.9
Calculation of frequency of dessert production:
It is calculated by dividing the annual demand with the batch quantity.
Hence, the company will produce 100 batches.
b
Interpretation:
Order size required to minimize the total annual cost and amount of savings by using order size.
Concept Introduction: Materials Requirement Planning is a process in which planning is made for the requirement of raw material required for manufacturing of the finished product.
b

Explanation of Solution
Calculation of order size:
It is calculated by dividing two values and taking the square root of the attained value. First value is the multiple of annual demand and set up cost with 2. Second value is calculated by multiplying the holding cost with the value attained by subtracting the dividing value of daily demand with production rate from 1.
Hence, the economic order quantity is 762.5
Calculation of total holding cost and ordering cost for optimal order quantity:
It is given that the optimal order quantity is 762.5 desserts.
Annual holding cost is calculated by multiplying the holding cost with two values. First value is calculated by dividing the quantity with 2. Second value is calculated by subtracting the value attained by dividing the daily demand with the production from 1.
Hence, the annual holding cost is $157.38
Calculation of annual ordering cost:
It is calculated by multiplying the setup cost with the value attained by dividing the annual demand with the batch quantity.
Hence, the annual ordering cost is $157.37
Calculation of total cost of inventory:
It is calculated by adding annual holding cost and annual ordering cost.
Annual saving in the total cost of optimal order quantity:
It is calculated by subtracting the total cost of optimal quantity from the total cost of given batch quantity.
Hence, the annual saving is $147.2
c
Interpretation:
Change in size of refrigerated pantry.
Concept Introduction: The efficiency of output is the actual productivity generated compared with the planned or effective capacity. It is usually calculated by dividing actual output by effective capacity.
c

Explanation of Solution
The plan to expand the capacity
The lowest inventory cost order size is 762 desserts. However, the refrigerator can only store 300 desserts. Thus, the capacity must increase 462 spaces.
Want to see more full solutions like this?
Chapter 10 Solutions
Practical Operations Management
- The Big Buy Supermarket stocks Munchies Cereal. Demand for Munchies is 4,000 boxes peryear (365 days). It costs the store $60 per order of Munchies, and it costs $0.80 per box per yearto keep the cereal in stock. Once an order for Munchies is placed, it takes 4 days to receive theorder from a food distributor. Determine The optimal order sizearrow_forwardThe Rainwater Brewery produces Rainwater Light Beer, which it stores in barrels in its warehouse and supplies to its distributors on demand. The demand for Rainwater is 1,500 barrels of beer per day (365 days per year). The brewery can produce 2,000 barrels of Rainwater per day. It costs $6,500 to set up a production run for Rainwater. Once it is brewed, the beer is stored in a refrigerated warehouse at an annual cost of $50 per barrel. Determine the economic order quantity and the minimum total annual inventory cost.arrow_forwardThe local supermarket buys lettuce each day to ensure really fresh produce. Each morning any lettuce that is left from the previous day is sold to a dealer that resells it to farmers who use it to feed their animals. This week the supermarket can buy fresh lettuce for $9.00 a box. The lettuce is sold for $17.00 a box and the dealer that sells old lettuce is willing to pay $5.00 a box. Past history says that tomorrow's demand for lettuce averages 258 boxes with a standard deviation of 41 boxes. How many boxes of lettuce should the supermarket purchase tomorrow? (Round your answer to the nearest whole number.) Number of boxes ???arrow_forward
- The local supermarket buys lettuce each day to ensure really fresh produce. Each morning any lettuce that is left from the previous day is sold to a dealer that resells it to farmers who use it to feed their animals. This week the supermarket can buy fresh lettuce for $4.00 a box. The lettuce is sold for $16.00 a box and the dealer that sells old lettuce is willing to pay $2.50 a box. Past history says that tomorrow's demand for lettuce averages 252 boxes with a standard deviation of 34 boxes. How many boxes of lettuce should the supermarket purchase tomorrow? (Round your answer to the nearest whole number.)arrow_forwardThe local supermarket buys lettuce each day to ensure really fresh produce. Each morning any lettuce that is left from the previous day is sold to a dealer that resells it to farmers who use it to feed their animals. This week the supermarket can buy fresh lettuce for $11.00 a box. The lettuce is sold for $25.00 a box and the dealer that sells old lettuce is willing to pay $3.00 a box. Past history says that tomorrow's demand for lettuce averages 265 boxes with a standard deviation of 42 boxes. How many boxes of lettuce should the supermarket purchase tomorrow? (Use Excel's NORMSINV() function to find the Z-score. Round intermediate calculations to four decimal places. Round your answer to the nearest whole number.) Number of boxes ( ? )arrow_forwardA toy manufacturer uses 48,000 rubber wheels per year for its popular dump truck series. The firm makes its own wheels, which it can produce at a rate of 800 per day. The toy trucks are assembled uniformly over the entire year. Carrying cost is $1 per wheel a year. Set-up cost for a production run of wheels is $45. The firm operates 240 days per year. Determine optimal run size The minimum total annual cost for carrying and set-uparrow_forward
- An insurance company has custom envelopes printed for correspondence with its clients. It uses 780 boxes of envelopes annually at a steady rate. It costs $285 for delivery and processing (in addition to the printing costs) each time the company places an order, and it costs $2 per box for annual storage. To minimize costs, how many boxes of envelopes should the company order?arrow_forwardHolstein Computing manufactures an inexpensive audio card (Audio Max) for assembly into several models of its microcomputers. The annual demand for this part is 100,000 units. The annual inventory carrying cost is $5 per unit and the cost of preparing an order and making production setup for the order is $750. The company operates 250 days per year. The machine used to manufacture this part has a production rate of 2000 units per day. Please keep two digits after the decimal and don't omit 0 before the decimal, e.g., 0.78 1. How many orders are produced in a year? 2. What is the maximum inventory for Audio Max? 3. How long is the production run for each order? 4. What is the total annual cost of preparing the orders and making the setups for Audio Max?arrow_forwardThe materials manager for a billiard ball maker must periodically place orders for resin, one of the raw materials used in producing billiard balls. She knows that manufacturing uses resin at a rate of 50 kilograms each day, and that it costs $.04 per day to carry a kilogram of resin in inventory. She also knows that the order costs for resin are $100 per order, and that the lead time for delivery is four days. If the order size was 1,000 kilograms of resin, what would be the average inventory level?arrow_forward
- A firm uses a fixed time period model to manage a type of bolts they keep in inventory. The average daily demand for the bolts is 53 with a standard deviation of 6. An order is placed every 35 days and is received 2 days later. They use a 99 percent service level and currently have 92 on hand. How many should they order? Do not round intermediate calculations. Round your answer to a whole number. Your Answer: Answerarrow_forwardThe local supermarket buys lettuce each day to ensure really fresh produce. Each morning any lettuce that is left from the previous day is sold to a dealer that resells it to farmers who use it to feed their animals. This week the supermarket can buy fresh lettuce for $4.00 a box. The lettuce is sold for $10.00 a box and the dealer that sells old lettuce is willing to pay $1.50 a box. Past history says that tomorrow’s demand for lettuce averages 250 boxes with a standard deviation of 34 boxes. How many boxes of lettuce should the supermarket purchase tomorrow?arrow_forwardThe Petroco Company uses a highly toxic chemical in one of its manufacturing processes. It must have the product delivered by special cargo trucks designed for safe shipment of chemicals. As such, ordering (and delivery) costs are relatively high, at $2,600 per order. The chemical product is packaged in 1-gallon plastic containers. The cost of holding the chemical in storage is $50 per gallon per year. The annual demand for the chemical, which is constant over time, is 2,000 gallons per year. The lead time from time of order placement until receipt is 10 days. The company operates 310 working days per year. Compute the optimal order quantity, the total minimum inventory cost, and the reorder point.arrow_forward
- Practical Management ScienceOperations ManagementISBN:9781337406659Author:WINSTON, Wayne L.Publisher:Cengage,
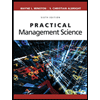