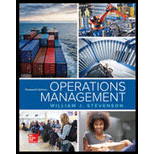
Operations Management
13th Edition
ISBN: 9781259667473
Author: William J Stevenson
Publisher: McGraw-Hill Education
expand_more
expand_more
format_list_bulleted
Concept explainers
Textbook Question
Chapter 11, Problem 9P
Wormwood, Ltd., produces a variety of furniture products. The planning committee wants to prepare an aggregate plan for the next six months using the following information.
Subcontracting can handle a maximum of 10 units per month. Beginning inventory is zero. Develop a plan that minimizes total cost. No back orders are allowed. Regular capacity = Regular production.
Expert Solution & Answer

Want to see the full answer?
Check out a sample textbook solution
Students have asked these similar questions
WSS company makes weatherproof surveillance systems for parking lots. Demand estimates for the next four quarters are 25, 9, 13, and 17 units. Prepare an aggregate plan that uses inventory, regular time and overtime and back orders. Subcontracting is not allowed. Regular time capacity is 15 units for quarters 1 and 2, 18 units for quarters 3 and 4. Overtime capacity is 3 units per quarter. Regular time cost is $2000 per unit, while overtime cost is $3000 per unit. Back order cost is $300 per unit per quarter; inventory holding cost is $100 per unit per quarter. Beginning inventory is zero.
Questions
At the end of quarter 3, what is the ending inventory of finished systems? Answer: No ending Inventory =0
What is the total cost? 15*2000 + 6*2300 +4*2600 + 9*2000 + 13*2000 + 17*2000 =$132, 200
What is the average cost per unit? Answer 132200 / 64 = $2,066.
WSS company makes weatherproof surveillance systems for parking lots. Demand estimates for the next four quarters are 25, 9, 13, and 17 units. Prepare an aggregate plan that uses inventory, regular time, and over time, and backorders. Subcontracting is not allowed. The regular time capacity is 15 units for quarters 1 and 2, 18 units for quarters 3 and 4. Overtime capacity is 3 units per quarter. The regular time cost is $2000 per unit, while the overtime cost is $3000 per unit. Backorder costs $300 per unit per quarter; inventory holding costs $100 per unit per quarter. The beginning inventory is zero.
How many total units will be produced in quarter 1 for delivery in quarter 1?
How many units in total will be used to fill back orders over the four quarters?
What is the cost to produce one unit in Quarter 4 using overtime to fill a back order in quarter one?
JAYB, manager of a Fabrication company, has the following aggregate demand requirements and other data for the upcoming four quarters.
Table 5: Forecast and cost information
[Jadual 5: Maklumat Ramalan dan kos]
Quarter
[Suku]
Demand
[Permintaan]
Previous quarter's output
[Keluaran suku sebelumnya]
1,500 units
1
1,400
Beginning inventory
[Inventori awal]
200 units
2
1,000
Hiring workers
[Pengambilan pekerja]
RM6 per unit
3
1,500
Laying off workers
[Pembuangan pekerja]
RM11 per unit
4
1,300
Unit cost
[Kos unit]
RM30 per unit
With the information given, JAYB wants you to calculate the total cost of using chase strategy by hiring and layoff workers.
Chapter 11 Solutions
Operations Management
Ch. 11 - What three levels of planning involve operations...Ch. 11 - What are the three phases of intermediate...Ch. 11 - Prob. 3DRQCh. 11 - Why is there a need for aggregate planning?Ch. 11 - What are the most common decision variables for...Ch. 11 - Prob. 6DRQCh. 11 - Briefly discuss the advantages and disadvantages...Ch. 11 - What are the primary advantages and limitations of...Ch. 11 - Briefly describe the planning techniques listed as...Ch. 11 - What are the inputs to master scheduling? What are...
Ch. 11 - Prob. 11DRQCh. 11 - What general trade-offs are involved in master...Ch. 11 - Who needs to interface with the master schedule...Ch. 11 - How has technology had an impact on master...Ch. 11 - Service operations often face more difficulty in...Ch. 11 - Name several behaviors related to aggregate...Ch. 11 - Compute the total cost for each aggregate plan...Ch. 11 - A manager would like to know the total cost of a...Ch. 11 - Determine the total cost for this plan given the...Ch. 11 - a. Given the following forecast and steady regular...Ch. 11 - Manager T. C. Downs of Plum Engines, a producer of...Ch. 11 - Manager Chris Channing of Fabric Mills, Inc., has...Ch. 11 - SummerFun. Inc., produces a variety of recreation...Ch. 11 - Nowjuice, Inc., produces Shakewell fruit juice. A...Ch. 11 - Wormwood, Ltd., produces a variety of furniture...Ch. 11 - Refer to Solved Problem 1. Prepare two additional...Ch. 11 - Refer to Solved Problem 1. Suppose another option...Ch. 11 - Prob. 12PCh. 11 - Prob. 13PCh. 11 - Prob. 14PCh. 11 - Prob. 15PCh. 11 - Refer to Example 3. Suppose that regular-time...Ch. 11 - Prob. 17PCh. 11 - Prob. 18PCh. 11 - Prepare a master production schedule for...Ch. 11 - Update the master schedule shown in Figure 11.11...Ch. 11 - Prepare a master schedule like that shown in...Ch. 11 - Determine the available-to-promise (ATP)...Ch. 11 - Prepare a schedule like that shown in Figure 11.12...Ch. 11 - The objective is to choose the plan that has the...Ch. 11 - Prob. 2CQ
Knowledge Booster
Learn more about
Need a deep-dive on the concept behind this application? Look no further. Learn more about this topic, operations-management and related others by exploring similar questions and additional content below.Similar questions
- The president of Hill Enterprises, Terri Hill, projectsthe firm’s aggregate demand requirements over the next 8 monthsas follows:Jan. 1,400 May 2,200Feb. 1,600 June 2,200Mar. 1,800 July 1,800Apr. 1,800 Aug. 1,800 Her operations manager is considering a new plan, whichbegins in January with 200 units on hand. Stockout cost of lostsales is $100 per unit. Inventory holding cost is $20 per unit permonth. Ignore any idle-time costs. The plan is called plan A.Plan A: Vary the workforce level to execute a strategy thatproduces the quantity demanded in the prior month. TheDecember demand and rate of production are both 1,600 unitsper month. The cost of hiring additional workers is $5,000 per100 units. The cost of laying off workers is $7,500 per 100 units.Evaluate this plan.arrow_forwardThe president of Hill Enterprises, Terri Hill, projects the firm's aggregate demand requirements over the next 8 months as follows: alculator DEPREFERESSESES Cara be Her operations manager is considering a new plan, which begins in January with 200 units of inventory on hand. Stockout cost of lost sales is $65 per unit. Inventory holding cost is $20 per unit per month. Ignore any idle-time costs Evaluate the following plan. This exercise contains only Plan E. Plan E: Keep the current workforce, which is producing 1,600 units per month, and subcontract to meet the rest of the demand. Subcontract cost is $75 per unit. mummill M Pla $100433443 January February March April MESS Month 0 December 1 January 2 February 3 March 4 April 5 May 6 June 7 July 8 August Ask my instructor 1,400 1,600 1,800 1,800 Demand 1.400 1,600 1,800 1,800 2,200 2,100 1,800 1.400 May June July August Production (Units) 1,600 1,600 1,600 1,600 1,600 1,600 1,600 1,600 2,200 2.100 1.800 1,400 S Plan E Subcontract…arrow_forwardThe total cost, excluding normal time labor costs, for Plan A = $. (Enter your response as a whole number.) Plan B: Vary the workforce to produce the prior month's demand. Demand was 1,300 units in June. The cost of hiring additional workers is $30 per unit produced. The cost of layoffs is $65 per unit cut back. (Enter all responses as whole numbers.) Note: Both hiring and layoff costs are incurred in the month of the change (i.e., going from production of 1,300 in July to 1000 in August requires a layoff (and related costs) of 300 units in August). Month 1 2 3 September 4 October July August 5 November 6 December Demand 1000 1200 1400 1800 1800 1800 Hire Production (Units) The total hiring cost = $ The total layoff cost = $ The total inventory carrying The total stockout cost = $ The total cost, excluding normal time labor costs, for Plan B = (Enter your response as a whole number.) (Enter your response as a whole number.) cost = $ (Enter your response as a whole number.) Layoff…arrow_forward
- EE Company has the following aggregate demand requirements and data for the upcoming four quarters. Which of the following production plans has lower cost, Plan A using chase demand or Plan B using pure level strategy or C using 1350 level with subcontracting if needed. * Period 1 Demand Previous output 1300 units 1 1,400 Beginning Inventory 0 units 1,200 Inventory holding cost P10.00 3. 1,600 Hiring workers P40.00 1,500 Stockout cost P50.00 Firing workers Subcontracting cost P80.00 P60.00 Unit cost P30.00 Overtime P15.00 Plan A Plan B Plan C 2m4 OOOarrow_forwardPlanners for a company that makes several models of skateboards are about to prepare the aggregate plan that will cover six periods. They have assembled the following information. Period 1 2 3 4 5 6 Total Forecast 200 200 300 400 500 200 1,800 Costs Output Regular time=$2 per skateboard Overtime =$3 per skateboard Subcontract =$6 per skateboard Inventory =$1 per skateboard per period on average inventory Back orders =$5 per skateboard per period They now want to evaluate a plan that calls for a steady rate of regular-time output, mainly using inventory to absorb the uneven demand but allowing some backlog. Prepare an aggregate plan and determine its cost using the preceding information.arrow_forward9. Wormwood, Ltd., produces a variety of furniture products. The planning committee wants to pre- pare an aggregate plan for the next six months using the following information. Month Cost Per Unit Demand Capacity Regular Overtime 1 2 3 160 150 160 150 150 10 10 4 180 170 5 6 140 150 150 160 160 0 10 10 10 Regular time Overtime Subcontract Inventory holding, per month $50 75 80 4 Subcontracting can handle a maximum of 10 units per month. Beginning inventory is zero. Develop a plan that minimizes total cost. No back orders are allowed. Regular capacity = Regular production.arrow_forward
- 3) AGGREGATE PLANNING Mark Tuan, Operations Manager at GOT7 Furniture, has received the following estimates of demand requirements: January 1,100 February 1,200 March 1,400 April 1,800 May 1,800 June 1,600 Assuming stockout costs for lost sales of RM100 per unit, inventory carrying costs of RM25 per unit per month, and a zero beginning and ending inventory. Analyze the extra cost if the company vary the workforce, which performs at a current production level of 1,300 units per month. The cost of hiring additional workers is RM3,000 per 100 units produced. The cost of layoffs is RM6,000 per 100 units cut back.arrow_forwardThe factors are the most often used for manufacturing aggregate planning?In the context of a service?arrow_forwardYou have developed the following simple product structure of items needed for your gift bag for a rush party for prospective pledges in your organization. You forecast 200 attendees. Assume that there is no inventory on hand of any of the items. Explode the bill of material (BCOM). J К (2) L (3) М4) How many of L is needed? 1,200 300 600 900 1,800arrow_forward
- Given the projected demands for the next six months, prepare aggregate plan must wind up with no units in ending inventory in Period 6. Regular time capacity is 150 units per month. Overtime cost is $20 per unit, backorder cost is $30 per unit, inventory holding cost is $10 per unit based on maximum, subcontracting cost is $40 per unit, regular time cost of $20 per unit, and beginning inventory is 10. Month 1 2 3 45 6 Forecast 150 170 140 160 130 160 a. Prepare an aggregate plan with inventory and backlog allowed. Overtime and subcontracting are not allowed. b. Prepare an aggregate plan if the management decided to switch to chase strategy. They only allow backlog if absolutely needed. Regular production capacity is now 160.arrow_forwardTable below provides the demand forecast and production day information for an aggregate plan. Assume that no back orders are allowed in this case. Month January February March April May June Demand Forecast 3,000 4,500 3,400 2,500 4,000 3,200 Production Days 22 18 21 21 22 20 The costing information that is used to evaluate the total cost of each plan is as follows:• Inventory carrying cost: $4 per unit per month• Subcontracting cost per unit: $15 per unit• Working hours: 8 hours per day• Average pay rate: $12 per hour ($96 per day per worker)• Labour-hours to produce a unit: 2 hours per unit• Cost of increasing daily production rate (hiring and training): $300 per unit• Cost of decreasing daily production rate (layoffs): $700 per unitUse these information to formulate an aggregate plan. The firm would like to use level strategy: constant workforce for the aggregate planning. The firm chooses the average demand of the…arrow_forwardDirections Select one of these concepts: How the Aggregate Operations Plan combines required materials, capacity, and staffing. Inputs and application of the different Production Planning Strategies: Chase strategy, level strategy, Stable workforce Aggregate planning techniques that minimize the costs of operations. Application of Materials Requirement Planning methods as a manufacturing scheduling tool Use of Bills of Materials and Lot Sizing in MRP systemsarrow_forward
arrow_back_ios
SEE MORE QUESTIONS
arrow_forward_ios
Inventory Management | Concepts, Examples and Solved Problems; Author: Dr. Bharatendra Rai;https://www.youtube.com/watch?v=2n9NLZTIlz8;License: Standard YouTube License, CC-BY