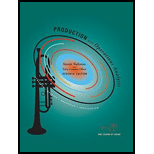
Concept explainers
a
To determine:
Minimum Constant workforce plan, hiring, firing and holding cost.
Introduction:
Linear program is a mathematical technique in which some variable maximized or minimized and some are kept constraint.
b
To determine:
Impact on cost if 1 month is required for training a new employee.
Introduction:
Linear program is a mathematical technique in which some variable maximized or minimized and some are kept constraint.
c
To determine:
Impact on cost if maximum number of emplyee can be hired is 10.
Introduction:
Linear program is a mathematical technique in which some variable maximized or minimized and some are kept constraint.
d
To determine:
Linear program for production level.
Introduction:
Linear program is a mathematical technique in which some variable maximized or minimized and some are kept constraint.
e
To determine:
Cost of the linear program
Introduction:
Linear program is a mathematical technique in which some variable maximized or minimized and some are kept constraint.
f
To determine:
Optimal plan subject to constraint.
Introduction
Optimal plan is a plan in which efficiency and effectiveness of all variables are maximized. It is a plan in which worker’s output is maximum while keeping cost and time minimized.

Want to see the full answer?
Check out a sample textbook solution
Chapter 3 Solutions
Production and Operations Analysis, Seventh Edition
- Scenario 4 Sharon Gillespie, a new buyer at Visionex, Inc., was reviewing quotations for a tooling contract submitted by four suppliers. She was evaluating the quotes based on price, target quality levels, and delivery lead time promises. As she was working, her manager, Dave Cox, entered her office. He asked how everything was progressing and if she needed any help. She mentioned she was reviewing quotations from suppliers for a tooling contract. Dave asked who the interested suppliers were and if she had made a decision. Sharon indicated that one supplier, Apex, appeared to fit exactly the requirements Visionex had specified in the proposal. Dave told her to keep up the good work. Later that day Dave again visited Sharons office. He stated that he had done some research on the suppliers and felt that another supplier, Micron, appeared to have the best track record with Visionex. He pointed out that Sharons first choice was a new supplier to Visionex and there was some risk involved with that choice. Dave indicated that it would please him greatly if she selected Micron for the contract. The next day Sharon was having lunch with another buyer, Mark Smith. She mentioned the conversation with Dave and said she honestly felt that Apex was the best choice. When Mark asked Sharon who Dave preferred, she answered, Micron. At that point Mark rolled his eyes and shook his head. Sharon asked what the body language was all about. Mark replied, Look, I know youre new but you should know this. I heard last week that Daves brother-in-law is a new part owner of Micron. I was wondering how soon it would be before he started steering business to that company. He is not the straightest character. Sharon was shocked. After a few moments, she announced that her original choice was still the best selection. At that point Mark reminded Sharon that she was replacing a terminated buyer who did not go along with one of Daves previous preferred suppliers. What should Sharon do in this situation?arrow_forwardScenario 4 Sharon Gillespie, a new buyer at Visionex, Inc., was reviewing quotations for a tooling contract submitted by four suppliers. She was evaluating the quotes based on price, target quality levels, and delivery lead time promises. As she was working, her manager, Dave Cox, entered her office. He asked how everything was progressing and if she needed any help. She mentioned she was reviewing quotations from suppliers for a tooling contract. Dave asked who the interested suppliers were and if she had made a decision. Sharon indicated that one supplier, Apex, appeared to fit exactly the requirements Visionex had specified in the proposal. Dave told her to keep up the good work. Later that day Dave again visited Sharons office. He stated that he had done some research on the suppliers and felt that another supplier, Micron, appeared to have the best track record with Visionex. He pointed out that Sharons first choice was a new supplier to Visionex and there was some risk involved with that choice. Dave indicated that it would please him greatly if she selected Micron for the contract. The next day Sharon was having lunch with another buyer, Mark Smith. She mentioned the conversation with Dave and said she honestly felt that Apex was the best choice. When Mark asked Sharon who Dave preferred, she answered, Micron. At that point Mark rolled his eyes and shook his head. Sharon asked what the body language was all about. Mark replied, Look, I know youre new but you should know this. I heard last week that Daves brother-in-law is a new part owner of Micron. I was wondering how soon it would be before he started steering business to that company. He is not the straightest character. Sharon was shocked. After a few moments, she announced that her original choice was still the best selection. At that point Mark reminded Sharon that she was replacing a terminated buyer who did not go along with one of Daves previous preferred suppliers. What does the Institute of Supply Management code of ethics say about financial conflicts of interest?arrow_forwardScenario 3 Ben Gibson, the purchasing manager at Coastal Products, was reviewing purchasing expenditures for packaging materials with Jeff Joyner. Ben was particularly disturbed about the amount spent on corrugated boxes purchased from Southeastern Corrugated. Ben said, I dont like the salesman from that company. He comes around here acting like he owns the place. He loves to tell us about his fancy car, house, and vacations. It seems to me he must be making too much money off of us! Jeff responded that he heard Southeastern Corrugated was going to ask for a price increase to cover the rising costs of raw material paper stock. Jeff further stated that Southeastern would probably ask for more than what was justified simply from rising paper stock costs. After the meeting, Ben decided he had heard enough. After all, he prided himself on being a results-oriented manager. There was no way he was going to allow that salesman to keep taking advantage of Coastal Products. Ben called Jeff and told him it was time to rebid the corrugated contract before Southeastern came in with a price increase request. Who did Jeff know that might be interested in the business? Jeff replied he had several companies in mind to include in the bidding process. These companies would surely come in at a lower price, partly because they used lower-grade boxes that would probably work well enough in Coastal Products process. Jeff also explained that these suppliers were not serious contenders for the business. Their purpose was to create competition with the bids. Ben told Jeff to make sure that Southeastern was well aware that these new suppliers were bidding on the contract. He also said to make sure the suppliers knew that price was going to be the determining factor in this quote, because he considered corrugated boxes to be a standard industry item. As the Marketing Manager for Southeastern Corrugated, what would you do upon receiving the request for quotation from Coastal Products?arrow_forward
- Scenario 3 Ben Gibson, the purchasing manager at Coastal Products, was reviewing purchasing expenditures for packaging materials with Jeff Joyner. Ben was particularly disturbed about the amount spent on corrugated boxes purchased from Southeastern Corrugated. Ben said, I dont like the salesman from that company. He comes around here acting like he owns the place. He loves to tell us about his fancy car, house, and vacations. It seems to me he must be making too much money off of us! Jeff responded that he heard Southeastern Corrugated was going to ask for a price increase to cover the rising costs of raw material paper stock. Jeff further stated that Southeastern would probably ask for more than what was justified simply from rising paper stock costs. After the meeting, Ben decided he had heard enough. After all, he prided himself on being a results-oriented manager. There was no way he was going to allow that salesman to keep taking advantage of Coastal Products. Ben called Jeff and told him it was time to rebid the corrugated contract before Southeastern came in with a price increase request. Who did Jeff know that might be interested in the business? Jeff replied he had several companies in mind to include in the bidding process. These companies would surely come in at a lower price, partly because they used lower-grade boxes that would probably work well enough in Coastal Products process. Jeff also explained that these suppliers were not serious contenders for the business. Their purpose was to create competition with the bids. Ben told Jeff to make sure that Southeastern was well aware that these new suppliers were bidding on the contract. He also said to make sure the suppliers knew that price was going to be the determining factor in this quote, because he considered corrugated boxes to be a standard industry item. Is Ben Gibson acting legally? Is he acting ethically? Why or why not?arrow_forwardGiven the following forecast and steady regular output of 550 every month, what total cost would result if overtime is limited to a maximum of 40 units a month, and subcontracting is limited to a maximum of 10 units a month? Unit costs are: Regular output $20 Overtime $30 Subcontract $25 Average Inventory $10 Backlog $18 Month 1 2 3 4 5 6 Forecast 540 540 570 590 650 680arrow_forwardDwayne Cole, owner of Florida firm that manufactures display cabinets, develops an 8-month aggregate plan. Demand and capacity (in units) are forecast as follows: Сараcity Jan Feb Mar Apr Маy Jun Jul Aug Source (Units) Regular 235 255 290 300 300 290 300 290 Time 30 19 Overtime 20 Subcontract 12 24 26 24 30 28 30 16 15 17 17 19 20 Demand 255 294 321 301 330 320 345 340 The cost of production each unit is $1000 on regular time, $1300 on overtime, and $1800 on a subcontract. Inventory carrying cost is $200 per unit per month. There is no beginning or ending inventory in stock, and no backorders are permitted from period to period. Let the production workforce vary by using regular time first, then overtime and then subcontracting. a) Set up a production plan that minimizes cost by producing exactly what the demand in each month. This plan allows no backorders or inventory. What is this plan's cost? b) Through better planning, regular time production can be set at exactly the same amount,…arrow_forward
- Identify some of the important short term and long term considerations in forecasting capacity requirements? Explain each point thoroughly. What steps can organizations take to ensure a realistic determination of capacity requirements?arrow_forwardplease help me with Question 3 thanks! Demand forecasts for 2021 are as follows: Month Demand Jan 140,000 Feb 78,900 Mar 85,800 Apr 89,100 May 123,600 Jun 136,350 Jul 120,450 Aug 106,950 Sep 121,950 Oct 135,750 Nov 87,000 Dec 93,300 Each worker can produce 900 products per month and is paid $1500 per month. Assume that at the end of last year, the company has 100 employees working on the production line. Hiring and layoff (firing) decisions are made at the beginning of each month, and associated costs are charged at that time. It costs the company $400 to hire and $800 to lay off a worker. The company incurs holding cost for the amount of ending inventory in each month, and incurs backorder cost at the end of each month for any unfilled orders. The company incurs $2 per month for holding one unit in inventory and $4 per unit backorder. 1 Prepare a level aggregate plan. Under this level aggregate plan, how…arrow_forwardDeforrest Marine Motors manufactures engines for the speedboat racing circuit. As part of their annual planning cycle, they forecasted demand for the next four quarters. The number of available days of production and the anticipated demand are given below. Employees Production Rate Production Cost Backorder Cost Overtime Cost Overtime Limit Demand Q1 2,400 6,019,000 They also estimated many of the costs required to conduct operations planning. Some of these key figures are listed below. 30 70 units/employee/quarter Q2 2,200 $1,000/unit $200/unit/quarter $1,500/unit <= 25% of Reg. Production Q3 1,700 Q4 1,800 Hire Cost Fire Cost Subcontracting Cost Subcontracting Limit Inventory Cost Initial Inventory $1,200/employee $800/employee $1,800/unit 400 units maximum $100/unit/quarter 280 units Deforrest Marine Motors wishes to maintain the current number of employees for the entire year to follow a level strategy balanced with inventory and backorders as needed. What is the total cost of this…arrow_forward
- Manager Chris Channing of Fabric Mills, Inc., has developed the forecast shown in the table for bolts of cloth. The figures are in hundreds of bolts. The department has a regular output capacity of 275(00) bolts per month, except for the seventh month, when capacity will be 240(00) bolts. Regular output has a cost of $43 per hundred bolts. Workers can be assigned to other jobs if production is less than regular. The beginning inventory is zero bolts. Month 1 2 3 4 5 6 7 Total Forecast 275 350 225 300 280 275 270 1,975 a. Develop a chase plan that matches the forecast and compute the total cost of your plan. Overtime is $68 per hundred bolts. Regular production can be less than regular capacity b. Would the total cost be less with full regular production each period with no overtime, but using a subcontractor to handle the excess above regular capacity at a cost of $53 per hundred bolts? Backlogs are not allowed. The inventory carrying cost is $2 per hundred bolts. (Round…arrow_forwardHickory Manufacturing Company forecasts the following demand for a product (in thousands of units) over the next five years. 1 2 3 4 5 86 90 Year Forecast demand Currently the manufacturer has seven machines that operate on a two-shift (eight hours each) basis. Thirty days per year are available for scheduled maintenance of equipment with no process output. Assume there are 250 workdays in a year. Each manufactured good takes 20 minutes to produce. a. What is the effective capacity of the factory? Round your answer down to the nearest whole number. units, year b. Given the five-year forecast, how much extra capacity is needed each year? Use a minus sign to enter an answer, if there is excess capacity, Round your answers to the nearest whole number. Year 1 Additional machines needed 2 1 24 Extra capacity needed (units) C. Does the firm need to buy more machines? If so, how many? When? If your answer is zero, enter "0". Round your answers up to the nearest whole number. 4 3 4 5 PEarrow_forwardBaker Manufacturing Company forecasts the following demand for a product (in thousands of units) over the next five years. Year 1 2 3 4 5 Forecast Demand 114 129 131 134 133 Currently, the manufacturer has eight machines that operate on a two-shift (eight hours each) basis. Twenty days per year are available for scheduled maintenance of equipment. Assume there are 250 workdays in a year. Each manufactured good takes 26 minutes to produce. a) What is the effective capacity of the factory? b) Given the five-year forecast, how much extra capacity is needed each year? c) Does the firm need to buy more machines? If so, how many? When? Solve manuallyarrow_forward
- Practical Management ScienceOperations ManagementISBN:9781337406659Author:WINSTON, Wayne L.Publisher:Cengage,Purchasing and Supply Chain ManagementOperations ManagementISBN:9781285869681Author:Robert M. Monczka, Robert B. Handfield, Larry C. Giunipero, James L. PattersonPublisher:Cengage Learning
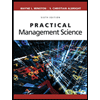
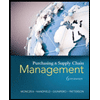