Human Resources Andrews Baldwin Chester Digby Erie Ferris Decisions Scientists - Recruitment & Retention $1,000 $1,200 $1,500 $1,500 $1,000 $900 Manufacturing - Training & $1,000 $1,200 $1,900 $1,000 $1,000 $500 Assembly Teams Sales - Compensation $1,000 $1,200 $1,900 $1,500 $1,000 $300 Total Expenditures $3,000 $3,600 $5,300 $4,000 $3,000 $1,700 Yearly Impacts R & D Cycle Time -2.5% -4% -6.3% -6.3% -2.5% -1.8% Demand 1.5% 1.8% 2.3% 2.3% 1.5% 1.3% Accessibility 4% 4.8% 7.6% 6% 4% 1.2% Productivity Index 2.5% 3% 4.8% 2.5% 2.5% 1.3% Turnover Rate -5% -10% -27.5% -15% -5% 11.5% Production After Adjustment -0.3% -0.1% 0.4% -0.3% -0.3% -0.6% Cumulative Impacts Andrews Baldwin Chester Digby Erie Ferris Material Cost -0.9% 0% -0.2% -1.2% -0.8% -0.1% R & D Cycle Time -6.5% -4.5% -5.9% -12.9% -8.8% -10.4% Labor Cost -2.6% 0% -0.6% -2.9% -2.2% -0.5% Demand 3.3% 2.8% 3.4% 3% 6.2% 3.9% Administrative Cost 0% -0.6% -2.3% 0% -13.3% -7% Accessibility 8.8% 7.6% 12.4% 10% 10% 2% Productivity Index 5.5% 4.8% 9.3% 6.3% 6.3% 2.3% Turnover Rate -15% -7.5% -40.5% -22.5% -22.5% 25.5% Production After Adjustment -0.4% -0.6% 0.8% -0.1% -0.1% -1.3% Custom Modules CP121037_1 Round: 3 Dec. 31, 2027 Workforce Summary Andrews Baldwin Chester Digby Erie Ferris Number of Employees 906 922 1,000 593 927 843 First Shift Second Shift 666 729 657 547 728 496 240 193 343 46 199 347 Overtime % 0% 0% 0% 0% 0% 0% Turnover Rate New Employees Separated Employees Productivity Index 8.5% 9.3% 6.0% 7.8% 7.8% 12.6% 243 85 246 292 192 269 0 126 0 0 0 0 105.5% 104.8% 109.3% 106.3% 106.3% 102.3% Total Quality Management Andrews Baldwin Chester Digby Erie Ferris Decisions Concurrent Engineering $0 $200 $300 $1,000 $0 $750 Quality Function Deployment Effort $0 UNEP Green Program $0 CCE (Concurrent Engineering)/6 $0 Sigma Training Channel Support Systems $0 aaaa $0 $300 $0 $0 $750 $0 $400 $0 $1,200 $0 $0 $600 $1,000 $1,000 $750 $0 $400 $0 $800 $750 CPI (Continuous Process $1,200 $0 $300 $1,000 $0 $0 Improvement) Systems Benchmarking $0 $0 $400 $0 $800 $750 GEMI TQEM Sustainability $0 $0 $500 $1,000 $1,200 $0 Vendor/JIT (Just in Time) Inventory $0 $300 $300 $0 $800 $0 QIT (Quality Initiative Training) $1,300 $200 $400 $1,000 $800 $0 Total Expenditures $2,500 $700 $3,900 $5,000 $6,600 $3,750 Yearly Impacts Material Cost -0.9% 0% -0.2% -1.2% -0.8% -0.1% R & D Cycle Time 0% -0.2% -0.9% -7.9% 0% -7.6% Labor Cost -2.6% 0% -0.6% -2.9% -2.2% -0.5% Demand 0% 0% 0.4% 0% 2.5% 1.4% Administrative Cost 0% -0.6% -2.3% 0% -13.3% -7%
Human Resources Andrews Baldwin Chester Digby Erie Ferris Decisions Scientists - Recruitment & Retention $1,000 $1,200 $1,500 $1,500 $1,000 $900 Manufacturing - Training & $1,000 $1,200 $1,900 $1,000 $1,000 $500 Assembly Teams Sales - Compensation $1,000 $1,200 $1,900 $1,500 $1,000 $300 Total Expenditures $3,000 $3,600 $5,300 $4,000 $3,000 $1,700 Yearly Impacts R & D Cycle Time -2.5% -4% -6.3% -6.3% -2.5% -1.8% Demand 1.5% 1.8% 2.3% 2.3% 1.5% 1.3% Accessibility 4% 4.8% 7.6% 6% 4% 1.2% Productivity Index 2.5% 3% 4.8% 2.5% 2.5% 1.3% Turnover Rate -5% -10% -27.5% -15% -5% 11.5% Production After Adjustment -0.3% -0.1% 0.4% -0.3% -0.3% -0.6% Cumulative Impacts Andrews Baldwin Chester Digby Erie Ferris Material Cost -0.9% 0% -0.2% -1.2% -0.8% -0.1% R & D Cycle Time -6.5% -4.5% -5.9% -12.9% -8.8% -10.4% Labor Cost -2.6% 0% -0.6% -2.9% -2.2% -0.5% Demand 3.3% 2.8% 3.4% 3% 6.2% 3.9% Administrative Cost 0% -0.6% -2.3% 0% -13.3% -7% Accessibility 8.8% 7.6% 12.4% 10% 10% 2% Productivity Index 5.5% 4.8% 9.3% 6.3% 6.3% 2.3% Turnover Rate -15% -7.5% -40.5% -22.5% -22.5% 25.5% Production After Adjustment -0.4% -0.6% 0.8% -0.1% -0.1% -1.3% Custom Modules CP121037_1 Round: 3 Dec. 31, 2027 Workforce Summary Andrews Baldwin Chester Digby Erie Ferris Number of Employees 906 922 1,000 593 927 843 First Shift Second Shift 666 729 657 547 728 496 240 193 343 46 199 347 Overtime % 0% 0% 0% 0% 0% 0% Turnover Rate New Employees Separated Employees Productivity Index 8.5% 9.3% 6.0% 7.8% 7.8% 12.6% 243 85 246 292 192 269 0 126 0 0 0 0 105.5% 104.8% 109.3% 106.3% 106.3% 102.3% Total Quality Management Andrews Baldwin Chester Digby Erie Ferris Decisions Concurrent Engineering $0 $200 $300 $1,000 $0 $750 Quality Function Deployment Effort $0 UNEP Green Program $0 CCE (Concurrent Engineering)/6 $0 Sigma Training Channel Support Systems $0 aaaa $0 $300 $0 $0 $750 $0 $400 $0 $1,200 $0 $0 $600 $1,000 $1,000 $750 $0 $400 $0 $800 $750 CPI (Continuous Process $1,200 $0 $300 $1,000 $0 $0 Improvement) Systems Benchmarking $0 $0 $400 $0 $800 $750 GEMI TQEM Sustainability $0 $0 $500 $1,000 $1,200 $0 Vendor/JIT (Just in Time) Inventory $0 $300 $300 $0 $800 $0 QIT (Quality Initiative Training) $1,300 $200 $400 $1,000 $800 $0 Total Expenditures $2,500 $700 $3,900 $5,000 $6,600 $3,750 Yearly Impacts Material Cost -0.9% 0% -0.2% -1.2% -0.8% -0.1% R & D Cycle Time 0% -0.2% -0.9% -7.9% 0% -7.6% Labor Cost -2.6% 0% -0.6% -2.9% -2.2% -0.5% Demand 0% 0% 0.4% 0% 2.5% 1.4% Administrative Cost 0% -0.6% -2.3% 0% -13.3% -7%
Pkg Acc Infor Systems MS VISIO CD
10th Edition
ISBN:9781133935940
Author:Ulric J. Gelinas
Publisher:Ulric J. Gelinas
Chapter14: The Human Resources (hr) Management And Payroll Processes
Section: Chapter Questions
Problem 7DQ
Related questions
Question
Final Individual Report
- List of team members and assigned organizational roles during different rounds of the simulation
- Identification of product/market segments on which strategy will be built
- Explanation of your team’s basic strategic approach (e.g., broad cost leader, niche differentiator with leading-edge technology, etc.), as well as your role in such decision-making process
- What functional strategies/decisions (i.e.,
accounting, finance, management , marketing, etc.) support your team’s overall strategic approach in each round - List of chosen success measures/performance criteria and accompanying weights, together with your analysis of the performance across all rounds of simulation
- You may choose any combination of success measures
- The stock price must be included and weighted no less than 20%
- Your peer-evaluation results and feedbacks; your learning on how to function well in team-settings
- Your overall summary of future learning and development plans
Note: only choose Erie reports

Transcribed Image Text:Human Resources
Andrews
Baldwin
Chester
Digby
Erie
Ferris
Decisions
Scientists - Recruitment & Retention
$1,000
$1,200
$1,500
$1,500
$1,000
$900
Manufacturing - Training &
$1,000
$1,200
$1,900
$1,000
$1,000
$500
Assembly Teams
Sales - Compensation
$1,000
$1,200
$1,900
$1,500
$1,000
$300
Total Expenditures
$3,000
$3,600
$5,300
$4,000
$3,000
$1,700
Yearly Impacts
R & D Cycle Time
-2.5%
-4%
-6.3%
-6.3%
-2.5%
-1.8%
Demand
1.5%
1.8%
2.3%
2.3%
1.5%
1.3%
Accessibility
4%
4.8%
7.6%
6%
4%
1.2%
Productivity Index
2.5%
3%
4.8%
2.5%
2.5%
1.3%
Turnover Rate
-5%
-10%
-27.5%
-15%
-5%
11.5%
Production After Adjustment
-0.3%
-0.1%
0.4%
-0.3%
-0.3%
-0.6%
Cumulative Impacts
Andrews
Baldwin
Chester
Digby
Erie
Ferris
Material Cost
-0.9%
0%
-0.2%
-1.2%
-0.8%
-0.1%
R & D Cycle Time
-6.5%
-4.5%
-5.9%
-12.9%
-8.8%
-10.4%
Labor Cost
-2.6%
0%
-0.6%
-2.9%
-2.2%
-0.5%
Demand
3.3%
2.8%
3.4%
3%
6.2%
3.9%
Administrative Cost
0%
-0.6%
-2.3%
0%
-13.3%
-7%
Accessibility
8.8%
7.6%
12.4%
10%
10%
2%
Productivity Index
5.5%
4.8%
9.3%
6.3%
6.3%
2.3%
Turnover Rate
-15%
-7.5%
-40.5%
-22.5%
-22.5%
25.5%
Production After Adjustment
-0.4%
-0.6%
0.8%
-0.1%
-0.1%
-1.3%

Transcribed Image Text:Custom Modules
CP121037_1
Round: 3 Dec. 31, 2027
Workforce Summary
Andrews
Baldwin
Chester
Digby
Erie
Ferris
Number of Employees
906
922
1,000
593
927
843
First Shift
Second Shift
666
729
657
547
728
496
240
193
343
46
199
347
Overtime %
0%
0%
0%
0%
0%
0%
Turnover Rate
New Employees
Separated Employees
Productivity Index
8.5%
9.3%
6.0%
7.8%
7.8%
12.6%
243
85
246
292
192
269
0
126
0
0
0
0
105.5%
104.8%
109.3%
106.3%
106.3%
102.3%
Total Quality Management
Andrews
Baldwin
Chester
Digby
Erie
Ferris
Decisions
Concurrent Engineering
$0
$200
$300
$1,000
$0
$750
Quality Function Deployment Effort
$0
UNEP Green Program
$0
CCE (Concurrent Engineering)/6
$0
Sigma Training
Channel Support Systems
$0
aaaa
$0
$300
$0
$0
$750
$0
$400
$0
$1,200
$0
$0
$600
$1,000
$1,000
$750
$0
$400
$0
$800
$750
CPI (Continuous Process
$1,200
$0
$300
$1,000
$0
$0
Improvement) Systems
Benchmarking
$0
$0
$400
$0
$800
$750
GEMI TQEM Sustainability
$0
$0
$500
$1,000
$1,200
$0
Vendor/JIT (Just in Time) Inventory
$0
$300
$300
$0
$800
$0
QIT (Quality Initiative Training)
$1,300
$200
$400
$1,000
$800
$0
Total Expenditures
$2,500
$700
$3,900
$5,000
$6,600
$3,750
Yearly Impacts
Material Cost
-0.9%
0%
-0.2%
-1.2%
-0.8%
-0.1%
R & D Cycle Time
0%
-0.2%
-0.9%
-7.9%
0%
-7.6%
Labor Cost
-2.6%
0%
-0.6%
-2.9%
-2.2%
-0.5%
Demand
0%
0%
0.4%
0%
2.5%
1.4%
Administrative Cost
0%
-0.6%
-2.3%
0%
-13.3%
-7%
Expert Solution

This question has been solved!
Explore an expertly crafted, step-by-step solution for a thorough understanding of key concepts.
Step by step
Solved in 2 steps

Recommended textbooks for you
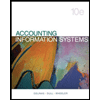
Pkg Acc Infor Systems MS VISIO CD
Finance
ISBN:
9781133935940
Author:
Ulric J. Gelinas
Publisher:
CENGAGE L
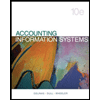
Pkg Acc Infor Systems MS VISIO CD
Finance
ISBN:
9781133935940
Author:
Ulric J. Gelinas
Publisher:
CENGAGE L