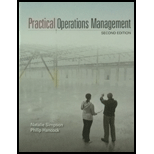
Concept explainers
a
Interpretation: Ending inventory at the end of month 4 is to be calculated.
Concept Introduction: Holding cost or inventory cost is the cost of warehousing in which unsold goods are kept. It includes transportation, warehousing, insurance etc.
a

Explanation of Solution
Demand of the product for 5 months is given as 200,50,200,200 and 150 respectively. Beginning inventory is 50 units and the company planned to produce 150 units per month for 5 months.
Calculation of inventories for next 5 months:
Month | 1 | 2 | 3 | 4 | 5 |
Demand | 200 | 50 | 200 | 200 | 150 |
Production | 150 | 150 | 150 | 150 | 150 |
Inventory on hand (50) | 0 | 100 | 50 | 0 | 0 |
The demand for the product is given and it is stated that units are planned for production for months. The beginning inventory is 50 units.
Calculation of ending inventory for month 1:
Ending inventory is calculated by adding beginning inventory and production. Then, subtract the attained value with demand of the product.
Hence, the ending inventory for the product is 0 units.
Hence, the same continues for all the months.
Calculation of ending inventory of month 4:
Ending inventory is calculated by adding beginning inventory and production. Then, subtract the attained value with the demand of the product.
Hence, the ending inventory for the product is 0 units.
b
Interpretation: Average inventory during the month of 2 is to be calculated.
Concept Introduction: Holding cost or inventory cost is the cost of warehousing in which unsold goods are kept. It includes transportation, warehousing, insurance etc.
b

Explanation of Solution
Calculation of average inventory during month 2:
Average inventory is calculated by taking the average of beginning and ending inventory of the certain period.
Hence, the average inventory for month 2 is 50 units.
c
Interpretation: Total inventory holding cost is to be calculated.
Concept Introduction: Holding cost or inventory cost is the cost of warehousing in which unsold goods are kept. It includes transportation, warehousing, insurance etc.
c

Explanation of Solution
Calculation of inventory holding cost:
It is given that the inventory holding cost per units is $0.50. Total inventory holding cost is calculated by multiplying the holding cost per unit with the sum of stock on hand over 5 months.
Hence, the total inventory holding cost is $75.
Want to see more full solutions like this?
Chapter 11 Solutions
Practical Operations Management
- As the production planner for Xiangling Hu Products, Inc., you have been given a bill of material for a bracket that is made up of a base, 2 springs, and 4 clamps. The base is assembled from 1 clamp and\ 1 housing. Each clamp has 1 handle and 2 castings.Each housing has 1 bearing and 2 shafts.There is no inventory on hand. C) Compute the net quantities needed if there are 25 of the base and 75 of the clamp in stock. (Product structure picture attached) Base = (?) units Spring = (?) units Clamp = (?) units Housing = (?) units Handle = (?) units Casting = (?) units Bearing = (?) units Shaft = (?) unitsarrow_forwardAs the production planner for Xiangling Hu Products, Inc., you have been given a bill of material for a bracket that is made up of a base, 2 springs, and 4 clamps. The base is assembled from 2 clamps and 1 housing. Each clamp has 1handle and 1 casting. Each housing has 2 bearings and 2 shafts. There is no inventory on hand. c) Compute the net quantities needed if there are 25 of the base and 100 of the clamp in stock. Base: units (enter your response as a whole number). Spring: units Clamp: units Housing: units Handle units Casting: units Bearing: units Shaft: unitsarrow_forwardSoutheast Soda Pop, Inc., has a new fruit drink for which it has high hopes. John Mittenthal, the production planner, has assembled the following cost data and demand forecast: demand forecast. Quarter Forecast 1 1,900 2 1,200 3 1,600 4 800 Costs/Other Data Previous quarter's output=1,200 cases Beginning inventory=0 cases Stockout cost of backorders=$160 per case Inventory holding cost=$40 per case at end of quarter Hiring employees=$35 per case Terminating employees=$80 per case Subcontracting cost=$65 per case Unit cost on regular time=$30 per case Overtime cost=$20 extra per case Capacity on regular time=1,900 cases per quarter John's job is to develop an aggregate plan. The three initial options he wants to evaluate are: • Plan A: a strategy that hires and fires personnel as necessary to meet the forecast. • Plan B: a level strategy. • Plan C: a level strategy that…arrow_forward
- In the context of an Accident and Emergency Department, high demand variation can be addressed by having: Select one alternative: Yield Management. Over staffing and preferential access. Marketing. Standby capacity and flexible staffing. Demand management.arrow_forwardSmart Manufacturing Company (SMC) manufactures a variety of products other than the drum components for printers. Their high selling mobile juicer cup JG-142 has the following expected demand sales figures (in units) over the coming six months: Month 2 3 4 5 Expected Demand (units) 17680 23040 21120 16640 21760 The following planning parameters apply: Current number of workers Output rate per worker Number of regular time hours Number of working days Regular time labour cost Overtime labour cost Planning Parameters 26 4 units/hour 8 hours/day 20 days/month Maximum overtime hours allowed Hiring cost (including training) Layoff cost Inventory carrying cost Backorder cost Opening inventory Planned ending inventory (end of month 6) Material Cost Subcontracting Cost with material Maximum subcontracting allowed $14.00 /hour $21.00 /hour 6 18300 20% of regular worker-hours/month $950 /worker $1780 /worker $1.75 /unit/month Total 118540 $7.00/unit backordered 400 units 900 units $15 /unit $35…arrow_forwardPlanners for a company that makes several models of skateboards are about to prepare the aggregate plan that will cover six periods. They have assembled the following information. Period 1 2 3 4 5 6 Total Forecast 200 200 300 400 500 200 1,800 Costs Output Regular time=$2 per skateboard Overtime =$3 per skateboard Subcontract =$6 per skateboard Inventory =$1 per skateboard per period on average inventory Back orders =$5 per skateboard per period They now want to evaluate a plan that calls for a steady rate of regular-time output, mainly using inventory to absorb the uneven demand but allowing some backlog. Prepare an aggregate plan and determine its cost using the preceding information.arrow_forward
- Below is a decision table for Gregor’s Tennis School. Director Gregor Anderson is considering expanding his school to accommodate the potential increased interest in youth tennis lessons, camps and teams. The decision table below describes his situation.Decision Table State of Nature Alternatives High Demand Moderate Demand Low Demand Add a new building 30,00030,000 9,5009,500 −35,000-35,000 Extend hours for existing building 25,00025,000 4,2004,200 −4,000-4,000 Do Nothing 00 00 00 Step 2 of 3: What is the estimated payoff for adding a new building during moderate demand?arrow_forwardAn engineering plant has developed the accompanying supply, demand, cost and inventory data. The engineering plant has a constant workforce and meets all its demands. Allocate production capacity to satisfy demand at a minimum cost. What is the cost of this plan? (Assume that back ordering is not a viable alternative for the plant) Demand forecast Period Demand (Unit) 1 650 2 700 3 900 Supply Capacity available (units) Period Regular time Overtime Subcontract 1 350 100 250 2 450 100 250 3 500 100 250 Other Data Initial Inventory 100 units Regular-time cost per unit R 50 Overtime cost per unit R 65 Subcontract cost per unit R 80 Carrying cost per unit per period R 1 Back order cost per unit per period R 4arrow_forwardNozone, Inc., a manufacturer of Freon recovery units (for automotive air conditioner maintenance), experiences a strongly seasonal demand pattern, driven by the summer air conditioning season. This year Nozone has put together a six-month production plan, where the monthly demands D, for recovery units are given in the table below. Each recovery unit is manufactured from one chassis assembly plus a variety of other parts. The chassis assemblies are produced in the machining center. Since there is a single chassis assembly per recovery unit, the demands in the table below also represent demands for chassis assemblies. The unit cost, fixed setup cost and monthly holding cost for chassis assemblies are also given in this table. The fixed setup cost is the firm's estimate of the cost to changeover the machining center to produce chassis assemblies, including labor and materials cost and the cost of disruption of other product lines. t D₁ C₁ A₁ h₂ 1 1,000 50 2,000 1 2 1,200 50 2,000 1 3 500…arrow_forward
- 1. Foxie Owl’s Besty Bagel shop makes fresh bagels. She has to buy raw materials fresh every day for selling on that day. She wants to know exactly how much should she spend on raw materials. Foxie did some analysis over the past month and came back with the following numbers: Daily demand was equally likely to be 200, 225, 250, 275, or 300 bagels. What should be the number of bagels on hand to satisfy a Fill Rate requirement of 96%, rounded to next integer value? Group of answer choices 300 275 286 263 2. Suppose that instead of a discrete demand distribution, Foxie’s shop determines that the daily demand for bagels is normally distributed, with a mean of 250 and a standard deviation of 35. Foxie still wants a Fill Rate of 98%. What is the appropriate level of on-hand inventory for Foxie’s shop? Group of answer choices 263 274 257 270arrow_forwardDemand for stereo headphones and MP3 players for joggers has caused Nina Industries to grow almost 50 percent over the past year. The number of joggers continues to expand, so Nina expects demand for headsets to also expand, because, as yet, no safety laws have been passed to prevent joggers from wearing them. Demand for the players for last year was as follows: MONTH DEMAND (UNITS) January 4,000 February 4,100 March 3,800 April 4,200 May 4,850 June 4,500 July 5,150 August 4,750 September 5,250 October 5,550 November 6,150 December 5,850 a. Using linear regression analysis, what would you estimate demand to be for each month next year? Using a spreadsheet, follow the general format in Exhibit 3.7. (picture below)(Do not round intermediate calculations. Round your answers to 2 decimal places.) Month Forecast january february march april may june july august september october november decemberarrow_forwardDemand for stereo headphones and MP3 players for joggers has caused Nina Industries to grow almost 50 percent over the past year. The number of joggers continues to expand, so Nina expects demand for headsets to also expand, because, as yet, no safety laws have been passed to prevent joggers from wearing them. Demand for the players for last year was as follows: MONTH DEMAND (UNITS) January 4,000 February 4,100 March 3,800 April 4,200 May 4,850 June 4,500 July 5,150 August 4,750 September 5,250 October 5,550 November 6,150 December 5,850 a. Using linear regression analysis, what would you estimate demand to be for each month next year? Using a spreadsheet, follow the general format in Exhibit 3.7. (picture below)(Do not round intermediate calculations. Round your answers to 2 decimal places.) Month Forecast january february march april may june july august september october november december b. To…arrow_forward
- Practical Management ScienceOperations ManagementISBN:9781337406659Author:WINSTON, Wayne L.Publisher:Cengage,
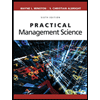