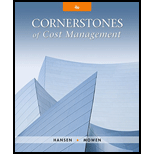
Lander Parts, Inc., produces various automobile parts. In one plant, Lander has a manufacturing cell with the theoretical capability to produce 450,000 fuel pumps per quarter. The conversion cost per quarter is $9,000,000. There are 150,000 production hours available within the cell per quarter.
Required:
- 1. Compute the theoretical velocity (per hour) and the theoretical cycle time (minutes per unit produced).
- 2. Compute the ideal amount of conversion cost that will be assigned per subassembly.
- 3. Suppose the actual time required to produce a fuel pump is 40 minutes. Compute the amount of conversion cost actually assigned to each unit produced. What happens to product cost if the time to produce a unit is decreased to 25 minutes? How can a firm encourage managers to reduce cycle time? Finally, discuss how this approach to assigning conversion cost can improve delivery time.
- 4. Assuming the actual time to produce one fuel pump is 40 minutes, calculate MCE. How much non-value-added time is being used? How much is it costing per unit?
- 5. Cycle time, velocity, MCE, conversion cost per unit (theoretical conversion rate × actual conversion time), and non-value-added costs are all measures of performance for the cell process. Discuss the incentives provided by these measures.
1.

Calculate the theoretical velocity and the theoretical cycle time.
Explanation of Solution
Cycle time: Cycle time and velocity are two operational “measures of responsiveness”. Cycle time is the span of time taken to produce a unit of output from the time the materials are received till the good is supplied to finished goods inventory. Therefore, cycle time is the time taken to produce a product.
Velocity: Velocity is the number of units of output that could be produced within a given period of time.
Calculate theoretical velocity:
Calculate theoretical cycle time:
2.

Calculate ideal amount of conversion cost assigned per subassembly.
Explanation of Solution
Conversion cost: The cost of changing the materials into a finished product. It includes direct labour costs and manufacturing overhead costs.
Calculate the conversion cost assigned per subassembly:
Working note:
(1)Calculate the conversion cost rate:
3.

Explain the manner in which this approach in assigning conversion cost can improve delivery time.
Explanation of Solution
The conversion cost assigned will be $25
Working note:
(2)Calculate applied conversion cost:
4.

Calculate MCE (manufacturing cycle efficiency), the non-value –added time used and calculate the costing per unit.
Explanation of Solution
Calculate manufacturing cycle efficiency:
Calculate wasted time:
Calculate the costing per unit:
5.

Briefly discuss the incentives provided by these measures.
Explanation of Solution
- Organizations must compete depending upon the time and cost in the advanced “manufacturing environment” and these objectives are supported by these measures. The aim is to reduce the cycle time by evading non-value added time.
- Since non-value-added time is decreased, manufacturing cycle efficiency is increased, and the conversion cost allocated per unit reduces. Likewise, as manufacturing cycle efficiency increases, a non-value-added time declines and non-value-added costs decrease, resulting in a lower-cost product.
Want to see more full solutions like this?
Chapter 13 Solutions
Cornerstones of Cost Management (Cornerstones Series)
- Hatch Manufacturing produces multiple machine parts. The theoretical cycle time for one of its products is 65 minutes per unit. The budgeted conversion costs for the manufacturing cell dedicated to the product are 12,960,000 per year. The total labor minutes available are 1,440,000. During the year, the cell was able to produce 0.6 units of the product per hour. Suppose also that production incentives exist to minimize unit product costs. Required: 1. Compute the theoretical conversion cost per unit. 2. Compute the applied conversion cost per minute (the amount of conversion cost actually assigned to the product). 3. Discuss how this approach to assigning conversion cost can improve delivery time performance. Explain how conversion cost acts as a performance driver for on-time deliveries.arrow_forwardThe one machine that used to produce both models has a capacity of 90,000 machine-hours per quarter. Fixed manufacturing costs per quarter are $800,000. a. Suppose that the maximum unit sales in a quarter that Pappy;s can acheive is 200,000 unit of each product. how many units of each model should Pappy's produce in a quarter? b. Supposed that the maximum unit sales in a quarter that Pappy's can acheive is 120,000 units of each product. How many units of each model should Pappy's produce in a quarter?arrow_forwardNelson Company's Radio Division currently is purchasing transistors from Charlotte Co. for $3.50 each. The total number of transistors needed is 8,000 per month. Nelson Company's Electronics Division can produce the transistors for a cost of $4.00 each, and it has plenty of capacity to manufacture the units. The $4.00 is made up of $3.25 in variable costs, and $0.75 in allocated fixed costs. The range of a possible transfer price should be Oa. $3.51 to $3.99 Ob. $3.25 to $3.50 Oc. $3.26 to $3.49 Od. $3.26 to $3.99arrow_forward
- Nelson Company's Radio Division currently is purchasing transistors from Charlotte Co. for $3.50 each. The total number of transistors needed is 8,000 per month. Nelson Company's Electronics Division can produce the transistors for a cost of $4.00 each, and it has plenty of capacity to manufacture the units. The $4.00 is made up of $3.25 in variable costs, and $0.75 in allocated fixed costs. The range of a possible transfer price should be a. $3.26 to $3.99 b. $3.51 to $3.99 c. $3.26 to $3.49 d. $3.25 to $3.50arrow_forwardIf 60,000 machine hours are available, and management desires to follow an optimal strategy, how many units of each product should the firm manufacture? How many units of each product should be purchased? With all other things constant, if management is able to reduce the direct material for an electric mixer to $23 per unit, how many units of each product should be manufactured? Purchased?arrow_forwardConnolly Company produces two types of lamps, classic and fancy, with unit contribution margins of $13 and $21, respectively. Each lamp must spend time on a special machine. The firm owns four machines that together provide 18,000 hours of machine time per year. The classic lamp requires 0.20 hours of machine time, the fancy lamp requires 0.50 hours of machine time. What is the total contribution margin of the optimal mix of classic and fancy lamps? $90,000 $1,170,000 $1,280,000 $950,000 $1,000,000arrow_forward
- Mighty Safe Fire Alarm is currently buying 57,000 motherboards from MotherBoard, Inc. at a price of $65 per board. Mighty Safe is considering making its own motherboards. The costs to make the motherboards are as follows: direct materials, $28 per unit; direct labor, $10 per unit; and variable factory overhead, $16 per unit. Fixed costs for the plant would increase by $80,000. Which option should be selected and why?arrow_forwardBarkov Industries makes an electronic component in two departments, Machining and Assembly. The capacity per month is 60,000 units in the Machining Department and 50,000 units in the Assembly Department. The only variable cost of the product is direct material of $200 per unit. All direct material cost is incurred in the Machining Department. All other costs of operating the two departments are fixed costs. Barkov can sell as many units of this electronic component as it produces at a selling price of $500 per unit. Required: a) Barkov’s Machining managers believe that they could increase the capacity in their department by 10,000 units, if they were able to increase fixed costs by $100,000. Should the money be spent? Explain.b) An outside contractor offers to do assembly for 10,000 units at a cost of $2,000,000. Should Barkov accept the offer from the subcontractor? Show calculations.c) How do your answers in parts (a) and (b) relate to the theory of constraints?…arrow_forwardBarkov Industries makes an electronic component in two departments, Machining and Assembly. The capacity per month is 60,000 units in the Machining Department and 50,000 units in the Assembly Department. The only variable cost of the product is direct material of $200 per unit. All direct material cost is incurred in the Machining Department. All other costs of operating the two departments are fixed costs. Barkov can sell as many units of this electronic component as it produces at a selling price of $500 per unit. Required: Barkov’s Machining managers believe that they could increase the capacity in their department by 10,000 units, if they were able to increase fixed costs by $100,000. Should the money be spent? Explain. An outside contractor offers to do assembly for 10,000 units at a cost of $2,000,000. Should Barkov accept the offer from the subcontractor? Show calculations. How do your answers in parts (a) and (b) relate to the theory of constraints? Explain.arrow_forward
- If answered within 40mins ,it would be helpful.I ll surely upvote. Assume that the motor manufacturer produces two types of drill motors (A-1 and A-2), and three types of saw motors(M-1, M-2, M-3). To setup the production line it would cost $12,000 for the drill motors and $8,000 for the new saw motors. The production capacity is 10,000 motors per period. Based on the information below determine the production quantity that should be planned for The M-3 type of saw motors only. Type Demand/Period Conversion Factor Initial Inventory Safety Stock A-1 3,000 1.10 100 40 A-2 2,000 0.95 200 20 M-1 1,000 1.15 100 20 M-2 4,000 1.05 500 50 M-3 2,500 0.90 100 30arrow_forwardA company makes two products A and B, using a CNC milling machine which is classified as a single resource pool. The resource is available for 900 minutes per day. The contribution margins for product A and B are $20 and $35 per unit respectively. The unit loads are 10 and 20 minutes per unit. The company wishes to produce a mix of 60% As and 40% Bs. At the indicated product mix, what is the financial capacity (profit per day)? hint: find a weighted margin per unit, then, multiply it by the effective capacity found in previous question. **$1,508.43 per day **$1,899.03 per day **$1,671.42 per day **$1,775.32 per dayarrow_forwardTriple X Company manufactures and sells refrigerators. It makes some of the parts for the refrigerators and purchases others. The engineering department believes it might be possible to cut costs by manufacturing one of the parts currently being purchased for $8.25 each. The firm uses 100,000 of these parts each year. The accounting department compiles the followinglist of costs based on engineering estimates:Fixed costs will increase by $50,000.Labor costs will increase by $125,000.Factory overhead, currently running $500,000 per year, may be expected to increase 12 percent. Raw materials used to make the part will cost $600,000.Given the preceding estimates, should Triple X make the part or continue to buy it?arrow_forward
- Cornerstones of Cost Management (Cornerstones Ser...AccountingISBN:9781305970663Author:Don R. Hansen, Maryanne M. MowenPublisher:Cengage Learning
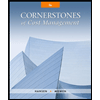